
Topic
Chronicle

ChronicleFeaturesOpinion
March 15, 2024
March 15, 2024
The irony of a tsunami
ChronicleFeaturesOpinion
January 15, 2024
January 15, 2024
Rupert Murdoch’s lessons for us

ChronicleFeaturesOpinion
November 6, 2023
November 6, 2023
No print type is ‘safe’

ChronicleFeaturesOpinionWide Format Week
August 25, 2023
August 25, 2023
Where have all the workers gone?
Advertisement
Stories continue below

ChronicleFeaturesOpinion
June 23, 2023
June 23, 2023
What’s in a name

ChronicleFeaturesOpinion
April 28, 2023
April 28, 2023
An unresolved shell game

ChronicleFeaturesOpinion
October 28, 2022
October 28, 2022
Something new for 33

ChronicleFeaturesOpinion
August 19, 2022
August 19, 2022
Uline’s challenge to naysayers

ChronicleFeaturesOpinion
June 24, 2022
June 24, 2022
The first Rolands in North America

ChronicleFeaturesOpinion
April 25, 2022
April 25, 2022
Alva and his newspaper

ChronicleFeaturesOpinion
February 25, 2022
February 25, 2022
Meet the younger Tanzer brother

ChronicleFeaturesOpinion
December 30, 2021
December 30, 2021
A tribute to Eric Tanzer

ChronicleFeaturesOpinion
November 18, 2021
November 18, 2021
Flute: Print’s golden goose

ChronicleFeaturesOpinion
October 7, 2021
October 7, 2021
Tripping over the obvious

ChronicleFeaturesOpinion
September 10, 2021
September 10, 2021
60 years of print

ChronicleFeaturesOpinion
July 29, 2021
July 29, 2021
A successful production model

ChronicleFeaturesOpinion
June 18, 2021
June 18, 2021
The art of being credible

ChronicleFeaturesOpinion
June 11, 2021
June 11, 2021
Two remarkable gentlemen from Winnipeg

ChronicleFeaturesOpinion
May 27, 2021
May 27, 2021
Wish you were here

ChronicleFeaturesOpinion
May 14, 2021
May 14, 2021
The ultimate disruptor
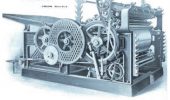
ChronicleFeaturesOpinion
April 16, 2021
April 16, 2021
When the next big thing … isn’t

ChronicleFeaturesOpinion
March 26, 2021
March 26, 2021
Cornering the market

ChronicleFeaturesOpinion
March 8, 2021
March 8, 2021
A chance encounter

ChronicleFeaturesOpinion
February 19, 2021
February 19, 2021
Fire and brimstone: The great awakening of John Thomson

ChronicleFeaturesOpinion
January 13, 2021
January 13, 2021
Stroke of genius

ChronicleFeaturesOpinion
December 2, 2020
December 2, 2020
2020’s best printing press?

ChronicleFeaturesOpinion
October 2, 2020
October 2, 2020
Not everything turns to gold

ChronicleFeaturesOpinion
July 30, 2020
July 30, 2020
What happens after COVID-19 for print?

ChronicleFeaturesOpinion
July 9, 2020
July 9, 2020
The importance of uniform world standards

ChronicleFeaturesOpinion
May 14, 2020
May 14, 2020
Operation Bernard: How the Nazis almost won the war with forgeries

ChronicleFeaturesOpinion
February 13, 2020
February 13, 2020
A stroke of genius

ChronicleFeaturesOpinion
December 5, 2019